Porosity in Welding: Identifying Common Issues and Implementing Best Practices for Prevention
Porosity in welding is a pervasive problem that commonly goes undetected till it causes considerable troubles with the honesty of welds. This usual problem can jeopardize the stamina and toughness of bonded frameworks, presenting security dangers and resulting in expensive rework. By recognizing the source of porosity and executing reliable prevention approaches, welders can significantly enhance the high quality and integrity of their welds. In this conversation, we will explore the crucial variables adding to porosity formation, examine its harmful impacts on weld performance, and go over the most effective methods that can be adopted to minimize porosity event in welding procedures.
Common Reasons For Porosity
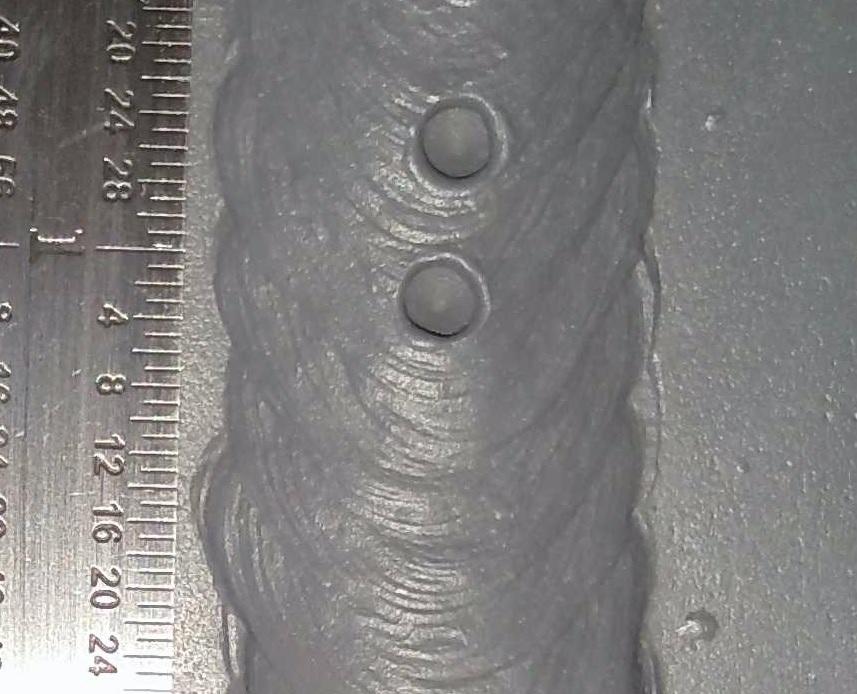
One more constant offender behind porosity is the visibility of contaminants on the surface area of the base metal, such as oil, oil, or corrosion. When these contaminants are not efficiently removed before welding, they can evaporate and end up being trapped in the weld, creating problems. Furthermore, using dirty or wet filler products can introduce contaminations into the weld, adding to porosity issues. To minimize these common sources of porosity, detailed cleaning of base metals, proper shielding gas choice, and adherence to ideal welding specifications are crucial practices in attaining high-grade, porosity-free welds.
Effect of Porosity on Weld Quality

The existence of porosity in welding can considerably compromise the structural stability and mechanical residential or commercial properties of bonded joints. Porosity develops spaces within the weld metal, deteriorating its overall strength and load-bearing capability. These spaces work as stress and anxiety focus factors, making the weld extra susceptible to breaking and failure under applied lots. In addition, porosity can lower the weld's resistance to official statement rust and various other ecological aspects, better lessening its long life and efficiency.
Welds with high porosity levels have a tendency to exhibit lower influence strength and decreased capacity to warp plastically before fracturing. Porosity can hamper the weld's capacity to efficiently send forces, leading to premature weld failing and potential security hazards in vital frameworks.
Best Practices for Porosity Prevention
To boost the architectural honesty and top quality of bonded joints, what certain steps can be executed to reduce the occurrence of porosity during the welding procedure? Making use of the correct welding technique for the specific product being bonded, such as adjusting the welding angle and weapon placement, can additionally avoid porosity. Regular inspection of welds and prompt removal of any type of issues recognized during the welding process are important practices to protect against porosity and generate my link top quality welds.
Value of Correct Welding Strategies
Carrying out appropriate welding techniques is paramount in making certain the structural integrity and quality of bonded joints, building on the structure of effective porosity prevention procedures. Welding methods directly influence the general strength and durability of the bonded structure. One key facet of proper welding strategies is keeping the correct heat input. Too much warm can lead to boosted porosity because of the entrapment of gases in the weld swimming pool. On the other hand, not enough warm might result in incomplete fusion, producing potential powerlessness in the joint. Additionally, utilizing the appropriate welding specifications, such as voltage, current, and travel rate, is essential for attaining sound welds with very little porosity.
Additionally, the option of welding procedure, whether it be MIG, TIG, or stick welding, ought to align with the details needs of the job to guarantee optimal results. Correct cleansing and preparation of the base metal, as well as choosing the appropriate filler material, are additionally necessary components of efficient welding strategies. By adhering to these best techniques, welders can lessen the threat of porosity formation and produce premium, structurally audio welds.

Examining and Quality Control Steps
Testing procedures are vital to spot and protect against porosity in welding, guaranteeing the strength and durability of the last item. Non-destructive screening approaches such as ultrasonic screening, radiographic testing, and visual inspection are commonly used to recognize prospective problems like her response porosity.
Post-weld assessments, on the other hand, evaluate the last weld for any type of issues, including porosity, and validate that it meets defined standards. Carrying out a comprehensive high quality control strategy that includes complete screening procedures and assessments is extremely important to reducing porosity problems and making sure the total high quality of bonded joints.
Conclusion
Finally, porosity in welding can be an usual issue that impacts the high quality of welds. By recognizing the usual reasons of porosity and implementing best methods for prevention, such as appropriate welding techniques and screening steps, welders can ensure high top quality and reliable welds. It is necessary to prioritize avoidance techniques to decrease the event of porosity and keep the honesty of bonded structures.
Comments on “What is Porosity in Welding: Essential Tips for Achieving Flawless Welds”